TC4鈦合金作為一種典型的 α-β 型兩相鈦合金,密度小、比強度高、耐蝕耐熱性能好,被廣泛應用于航空、航天、軍工等領域 。 隨著越來越多的鈦產品涌入民用領域,TC4鈦合金開始被廣泛研究。 國內多位學者通過高溫下TC4鈦合金的熱壓變形,研究了變形溫度及變形速率對材料流變應力的影響,并結合微觀組織演變確定了材料最佳變形溫度及變形速率范圍 。 寶鈦集團、西部鈦業等鈦產品生產制造企業采用不同的軋制工藝及熱處理工藝對TC4鈦合金板坯進行軋制實驗,通過對試樣進行金相分析和力學性能測試,探究了最優軋制工藝。 王牛俊等人對TC4鈦合金進行鍛造熱塑性變形加工,然后進行多火次換向熱軋變形,研究了其組織演變規律。 徐勇等人通過多道次軋制制備了高強度TC4鈦合金板材,比較分析了多道次換向軋制和單向軋制的TC4鈦合金室溫力學性能和微觀組織。 目前研究多圍繞在TC4鈦合金熱變形特性研究及軋制工藝開發方面,對于熱軋過程板坯溫度變化及其全流程溫度
控制方面研究鮮有報道。
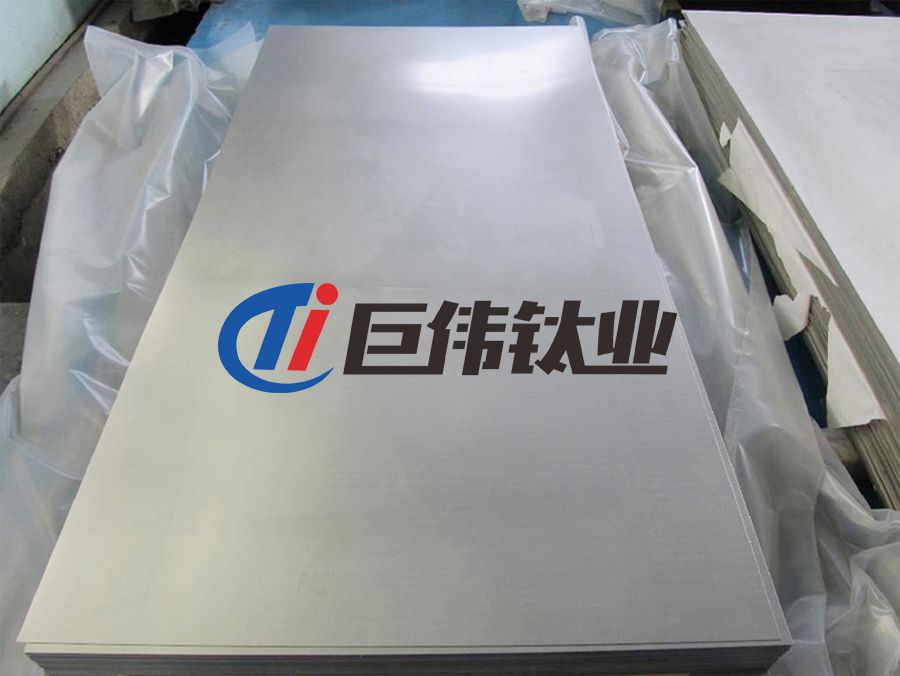
鈦合金軋制與常規鋼材軋制不同,其軋制溫度窗口窄,導熱性能差,若開軋溫度過高或軋制變形過大均會導致軋件心部溫度急劇升高,組織出現缺陷、塑性變差,導致軋制變形不均、板帶邊裂等問題;軋制溫度過低,將導致軋制力過大,板形難以控制等問題。 此外,軋制溫度也直接影響軋制力模型的準確性進而影響軋件出口厚度精度。
鈦合金板材熱軋生產目前仍依賴人工經驗,采用“邊看邊軋”方式,其自動化程度相比先進鋼鐵生產具有很大差距。 因此,系統研究多道次熱軋過程鈦合金板材溫度變化及分布規律,變形及力能參數變化等對于實現鈦合金板材生產自動化、提升產品良品率及生產效率至關重要。
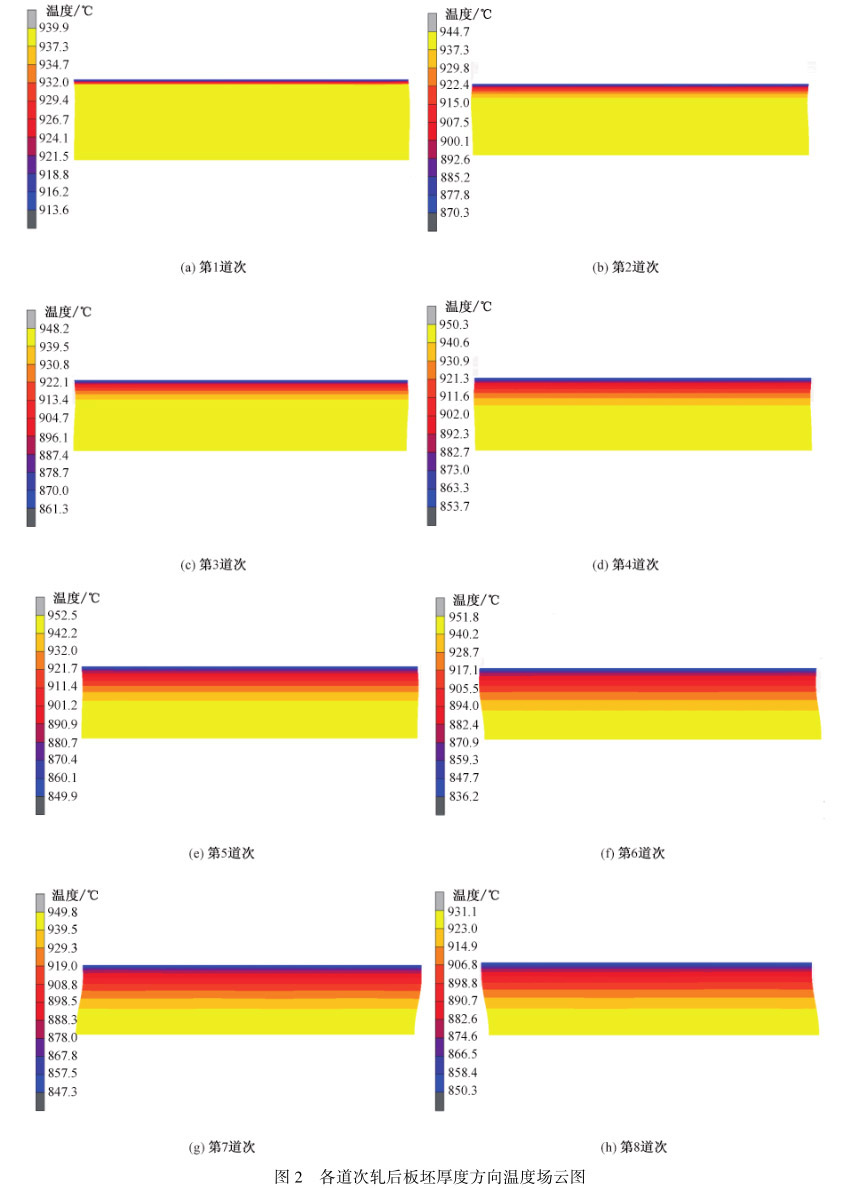
鈦合金板軋制過程中對溫度控制要求較為嚴格,故本文重點研究軋件心部溫度與表面溫度變化情況。 各道次軋后板坯厚度方向溫度場云圖分布如圖1。 隨著軋制道次的進行,鈦板坯溫降在厚度方向上逐漸由表面向心部推移,在板坯厚度較大時,表面溫度不斷降低,在第 7,8 道次由于軋件減薄內部熱傳導占據主要作用,表面溫度小幅升高;而心部溫度經 8 道次軋后變化不大。軋后板坯表面和心部平均溫度變化如圖2。
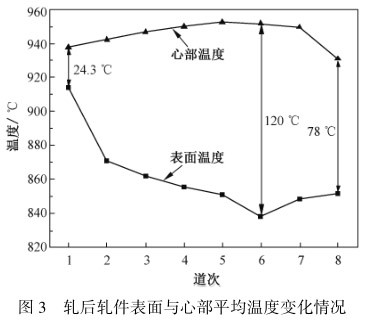
隨著軋制的進行,在初始幾個道次軋件較厚時,表面與心部溫差不斷增大,到第 6 道次最大溫差達到 120℃;而第 7 道次后軋件變薄,軋件內部熱傳導占據主導地位,軋件整體溫度開始趨于均勻,軋件表面溫度與心部溫度的溫差減小。
在鈦合金多道次軋制全流程中,隨著軋制道次的進行,軋件表面溫度與心部溫度的溫差呈先增大后較小的變化趨勢,在第6 道次軋件表面溫度與心部溫度的最大溫差可達 120℃。 表面溫差過大易形成較大熱應力從而導致表面開裂。
在各道次軋制時變形區內軋件心部溫度均由于塑性功變形生熱而升高,且心部溫度在前 5 道次不斷溫升,累計溫升約 20℃。 所以在TC4鈦合金熱軋一火次階段,軋件厚度較大時應控制道次壓下率不宜過大,一般不應超過 25%,以防板坯心部溫度越過相變點,塑性變差。
對比模擬得到的軋件表面溫度、各道次穩定軋制力與現場實測表面溫度、軋制力發現模擬結果均在允許誤差范圍內,說明本文建立的TC4 鈦合金板材多道次軋制有限元模型可靠,其分析結果對實際制定鈦合金多道次軋制工藝規程具有一定的指導意義。
相關鏈接